Introduction: A $400 Quad - Rebuilding a $240 1985 Yamaha Moto 4 Four Wheeler on the Cheap
I love building electric machines. I like how quiet they are, torquey, and efficient they can be. There's no gas to haul around or store and you can plug them in. But... I still love a good rumbling internal combustion engine. I had a 1987 Honda Fourtrax growing up in upstate NY and loved bombing around on our trails. I used that machine to grab buckets of sap during the spring, pull a small trailer filled with firewood during the winter, and to just have plain during the summer. My kiddos are growing up and I wanted them to try out some four wheeler power for themselves (helmets on, me driving to start of course) so I couldn't pass up the deal that popped up on Marketplace. Offered up was a 1985 Yamaha Moto 4 for $240. It was running, had all of the plastics (maybe not as solidified as one would want), and even had air in the tires! This was too good of a deal to pass up.
I wanted to take you on the short trip I just ventured to revive a still breathing icon of the four wheeler world. The first four wheeled ATV to hit the markets, setting the standard for "future" machines like my 87 Honda. I did this on the cheap and the total cost came in right around $400. It's not show worthy, nor are the parts all "Genuine Yamaha" or OEM, but it works, it's fun, and it didn't break the bank. This thing wasn't totally trash, but it was definitely heading down that road, I figured a few bucks and some sweat equity could really make a nearly trashed beast into 200cc's of treasure!
Supplies
Other than some random things I had already at the house (ignition switch, spray paint, bolts, front headlight) these were the only purchases that needed to be made to rebuild this beast.
Step 1: $240 Later - Bringing Home the Moto 4
As I mentioned earlier, $240 was a deal I just couldn't pass up. The guy I bought it from is the original owner, or better told it was in his family since it was first bought by his father. He had over 150 inquiries about the machine within the first few hours of it being posted but I told him I could head out right away with my trailer and pay him asking price. He liked the sounds of that and that is just what I did. It was running, so I first ripped around the driveway a few times to get my bearings with the machine and then rode it up into the trailer for the hour ride home.
He told me that the starter still probably worked since he was able to hook up a set of jumper cables and get it running off of a lawn tractor battery. The pull start was pretty wrecked and the pawls in it would only grab if you pulled on the handle just right... an electric start was definitely something I wanted to have. The plastics were not attached at all and were just floating around on the machine. Each hole's threads were rusted out or stripped completely, but the plastics were there, other than a few cracks and missing chunks. The machine was rusty, had a cracked frame, and a lot of quirks but once again, $240!!
Step 2: Stripping Down the Frame and Checking for Big Problems
Of course I had to ride it around a bit when I got it home, but not too much. For some reason Yamaha figured that the first four wheeler didn't need a suspension, anywhere. This thing is rigid across the board. That might explain the crack in the frame. Remarkably there was only one and it was an easy clean up and weld with my MIG.
I decided that I needed to clean up the frame since it was rusting all over the place. I stripped off the plastics (once again, not too hard since there was one bolt in total to remove) and then went at both the the plastics and the frame with a wire wheel on my angle grinder. This took off the loose paint and loose rust on both and prepped it for some painting.
Step 3: Repairing and Repainting the Plastics
The plastics were there but in rough shape. I decided to first fix any missing bits before repainting. I used an old plastic square shaped bucket and cut out a piece of plastic to fit over the front left fender since it was missing a big chunk. I then used some heavy duty rivets to hold it into place. My buddy suggested I plasti dipped the plastics and I figured that this was a good thing to test this stuff on. I had to use two cans to completely cover the plastics and the gas can. It came out pretty sharp, considering the amount of scratches and coats of paint the plasti dip had to cover. It gives it that rough and tumble look. After about three days the dip was pretty solid and there is little to no scraping off of the stuff.
Step 4: Refinishing the Frame
While the plastics were curing I prepped the frame for finishing. I used a metal primer first and then did three layers of bright blue magic... this was because it was what I had kicking around in the shop. Honestly, I like it. It's bright and funky all at once. I covered up the motor, carb, and other bits and pieces before spraying anything on the frame since I wasn't going to strip the frame of the motor and whatnot, I just wanted to prevent the frame from rusting further.
Step 5: Redrilling and Retapping Holes - Fitting the Plastics Again
As I mentioned earlier, all of the mounting holes for the plastics were completely rusted or stripped... well all but one. I figured the best way to remount the plastics would be to drill out and tap the holes with a larger diameter bolt, once again, whatever I had on hand. After redrilling and tapping each mounting point I put on the plastics and checked things for fit. Looking good!
Step 6: Building and Welding the Brush Guard / Tree Mover/remover
I am guessing they bought the base model Moto 4 because it didn't have any racks on it (and no seat or grip warmers... joking!). The front brush guard was in very rough shape and looked like it ended up becoming good friends with a few trees. I decided to use some free tube steel and bed rail to build a new brush guard / front rack. I used my MIG welder to put it all together and used similar joinery techniques as I had used to build my Ultra Robust Welding Cart.
First step was to cut the top bar of the old rack and tube notch (with a grinding wheel on the angle grinder) the current vertical tubes. I then determined the length of tube steel I wanted to use to make the front of the guard, cut that on the metal chopsaw and then cut another one for the top of the rack. I tube notched the middle section of the front of the rack and cut 45 degree cuts on the ends of the uprights and horizontals to join it all together.
I used a couple of welding magnets to keep things lined up and I used a level to determine where the connecting bars would go. These were connected to two pieces of bed rail that was drilled out to connect to the frame (where an original rack would have gone). The connecting tubes were directly connected to the main frame via a couple of tack welds to start. Once everything was leveled I finished the welds around the tubes and bolted the beast up.
I left the rack in the brushed raw steel and then I finished the rack with four coats of 2X matte clear enamel. I like the bright blue transition to old black and into raw brushed steel.
The rack can push through anything but it's always nice to have some brakes to prevent pushing through everything...
Step 7: New Front Brakes... Kinda
Amazingly the rear brake on the Moto 4 still worked, pretty well too. Front brakes would be a luxury that I thought I could quickly attach. The machine was missing the brake handle at the start and there were no brake lines to speak of. The machine utilizes the highest quality cable actuated brakes, so all I had to do was find the proper splitter cable on Ebay to connect to the front drums. Things were moving pretty slick until I realized that the brake bosses on the cast zinc hubs were both cracked, hence the missing cables! Well, I didn't want to buy new hubs quite yet so I decided that a couple of quick holds drilled through the brake cable mounting plate and into the remaining brake boss holes would suffice. I passed a cotter key through each hole and then used some wire to hold it all in place. There really is no need for crazy force here, just enough to keep things in place. The brakes work, well enough, and with some adjusting I am pretty sure I can get it stopping on a dime, maybe nickel? quarter? How about within five feet?
Step 8: New Electrical System
Honestly, up to this point things were moving WAY too smoothly. I had invested only four hours or so of effort into doing what I had done and was feeling pretty good about things! Enter the nearly 40 year old electrical system. Amazingly most of the wiring harnesses were still in place, but all of the switches other than the engine kill switch (thank God) were toast. I bought a new light/kill switch combo and a new battery (there was nothing present when I bought it). The fella I bought it from claimed the starter worked and when I tested it, it definitely was in complete working order. All I had to do was figure out how it all went together with what was present. I am color blind and the colors on the wires were pretty faded, so my wife and kids were a big help with identifying the wire colors. I found this great schematic for the machine online (the internet is magic) and was able to do most of the tracing with my multimeter set to continuity to figure where each wire was leading towards. Let me break down my work into manageable steps:
- I mounted the new switch to the handlebars and put on my fancy bright blue grips
- I ran a new positive battery wire to the original wire which ran to the starter motor (which was cut) and attached a new battery end terminal which would go to the solenoid
- There was no solenoid present so I scrounged up an old 12V solenoid from my old '67 Case tractor (which I no longer owned).
- I grounded the solenoid to the frame, ran negative battery wire from the battery and grounded that.
- The positive end of the battery was attached to the other side of the solenoid with a battery end terminal
- Then came the hard part of finding the right wire to act as the coil energizer. After a lot of trial and error and using the schematic (See pic) I was able to identify the right wire and attach it to the top of the solenoid (coil).
- I connected the correct wires at the front of the control switch and... nothing freaking happened!
- I took out the ole' multi and tested for voltage up front and lo and behold there was some, which brought my attention to the ignition key switch, which I figured was just as beat up as the rest of the rig.
- I had an ignition switch that I was originally going to use on one of my e-bikes but didn't like it for that application. It worked perfectly for the quad. I only wired it so that it would act as a break in the main circuit, identical to the schematic.
- I turned on the newly installed switch, flipped on the motor run switch on the handlebars and hit the start button and voila! It started right up.
- I could not figure out where they typically put the battery in this things so I decided to use some old foam mattress material (I love using this stuff) and cut a nice soft insulated battery container that slipped neatly and tightly into the frame between the rear support struts. I still need to cover up the battery connections, so don't brow beat me on that.
- The solenoid was mounted under the seat on the frame and I used that point as the main grounding point for the entire thing.
- I didn't get too fancy with the front light. I had one last LED light (the same used on my newest bike) which I simply bolted into the current light shroud. I wanted to keep the neutral switch light and oil temp light still working so it made the most sense to do it this way.
I think the pictures explain it well but I am more than happy to help you out if you have additional questions.
Step 9: Final Thoughts
And there it is. Literally under $400 and a mean looking machine! I am going to add a rear light at some point and maybe a rear rack too, but at the moment the kids and I are just loving riding it around the property. It's cool having such a classic machine that runs so spot on. I hope this inspires you to find that beater and make it into something fantastic!
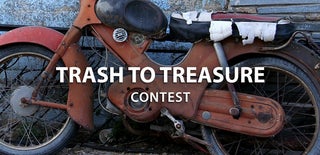
Runner Up in the
Trash to Treasure Contest
6 Comments
1 year ago
Good comprehensive job! I used what appears to be the same headlight on my 36v Ebike, powered at 10v by a down-convertor. I was surprised how good they were, definitely the best I've tried and dead cheap. I actually run it at 10v on my Ebike as I've found there's very little brightness difference (none?) between that and 13v but it takes quite a bit less current so it runs cooler and doesn't drain my battery so quickly. For my rear, I use a 12v MR16 LED downlighter with a normal red reflector over it in a reversed vintage bike headlight and run off the same down-convertor
Reply 1 year ago
Nice! I use the same light on my ebike too. Love how bright they are and how affordable they are too. I like the idea of running them on a lower voltage too. I have one more kicking around that I can tinker with so I might need to try a DC-DC convertor on it. Thanks for checking out my Instructable and for the comment!
Reply 1 year ago
(I'm putting this here for people who might not have used buck converters on lights but might be interested after following your thread)
I have a variable PSU with a current meter so it was easy to work out the optimium voltage for the headlights as being 10v.
Regarding DC buck converters, I became a bit of an expert by blowing them up! From my "experiments" I came to the following conclusions:
Don't match the input voltage to your ebike battery voltage- go over it as much as reasonably possible on the converter maximum input so long as it works also on your battery voltage. The reason is (a) my36v battery is actually at 42v when fully charged and (b) the converter input ranges can be a bit optimistic. Don't think 35v input is close enough to 36v just in case it does actually fry the circuit.
In the end I came across one that had a voltage input range of 6v-80v and an adjustable voltage in the range I needed. 80v may seem excessive but I've had it on now for over 3 years with no smoke yet. The one I bought was also in an aluminium box so it was protected and also had better heat loss but it was still very cheap (about £7/$8) but I can't find it now to reference. If not boxed, look at the size of the heatsink and ignore those with small ones. It also had an LED voltmeter in it, which isn't strictly necessary but made it easier to adjust rather than messing around with a voltmeter.
For the information of others: a buck converter is very efficient (over 90%) unlike a linear converter so less heat, plus less drain on a battery. e.g. a 3W 12V lamp will take approx. 0.25A@12v but a buck converter converts power so it will only take 0.25*12/36 or about 0.08A (0.1A allowing for inefficiency) from a 36v battery. A linear converter or a simple dropper resistor will still take 0.25A from the battery and will in fact be burning up twice as much power (6W) as the lamp itself and getting very hot.
Finally, you might think it's ok to string 3x identical 12v LED lamps in series to make up a 36v lamp. Again from my earlier "experiments" what seemed obvious wasn't. The control circuits in the MR16 bulbs didn't like it and one bulb would always blow quickly, hence the reason I went to the buck regulator and bulbs in parallel. This also had the advantage that I could use different lamps up to the buck regulator current maximum with no worries.
Reply 1 year ago
Fantastic information provided here! Love the learning by blowing up the components. Honestly, that's half the way I learn new things (safely of course). Thanks for giving such great details with this Instructable comment.
1 year ago
Great upgrade to the ATV :)
Reply 1 year ago
Thanks!